Multi-effect evaporators are one technology that has tremendously supported these two goals.
Multiple-Effect Evaporator for Maximization Efficiency and Savings
In terms of industrial processes, efficiency and cost savings are the most important criteria for operational efficiency. The multiple-effect evaporator (MEE) is one of the simplest but highly effective solutions for optimizing energy consumption and reducing waste. Because it is widely used in several industries, such as pharmaceuticals, chemicals, food processing, and wastewater treatment, this blog will look into how these systems work, their advantages, and their price effectiveness.
What does Multiple Affect Evaporator mean?
Multi-effect evaporators are systems designed to remove water from a solution effectively and efficiently, applying more effects or stages. This method involves energy savings compared with single-effect evaporators and is, therefore, the best option for industries that are concerned with either sustainability or cost-effectiveness.
How Does a Multiple Effect Evaporator Function?
The MEE plant uses steam to heat the feed solution and evaporate the water content. In each effect, the vapor produced thereby works as a heating medium in the incoming effect for energy-saving purposes. This cascading continues for several stages, which is advantageous in terms of efficiency and overall cost.
Essential Components of a Multiple Effect Evaporator
- Feed Tank: Hold the solution before entering the evaporator.
- Heating Chambers: Where steam transfers heat to the liquid.
- Evaporator Chambers: Facilitate the vaporization process.
- Condensers: Convert back any excess steam into a liquid for reuse.
- Vacuum System: Maintains optimal pressure conditions.
The Principle Behind Multiple-Effect Evaporators
The fundamental principle of an MEE is based on latent heat reuse. An MEE gains maximum thermal efficiency while requiring very little external energy input by using the vapor generated in one stage to heat the next stage. This design considerably reduces both fuel and operational costs.
Types of Feeding in a Multiple-Effect Evaporator
- Forward Feed: Ideal for temperature-sensitive materials.
- Backward Feed: Best for high-viscosity solutions.
- Mixed Feed: A combination of both methods for optimized performance.
The Multi-Effect Evaporators’ Merits Over the Single-Effect Evaporators
- Economical in Energy: Saving steam by avoiding to reuse of heating.
- Reduced Operating Costs: Less fuel and water needed.
- Higher Production Capacity: This can run continuously while improving throughput.
- Environmental Advantages: Produces less of a carbon footprint as energy waste is therefore reduced.
Cost of a Multiple Effect Evaporator
The cost of an MEE system varies based on:
- Some effects (more effects lead to greater savings but higher initial costs).
- Industry requirements (food, chemical, or wastewater applications).
- Customization options (materials, automation, and efficiency upgrades).
Multiple-Effect Evaporator Capacity
The MEEs come in different capacities, from small-scale installations for laboratory use to large-scale industrial systems that can handle thousands of liters per hour.
The Efficiency Calculation of Multiple-Effect Evaporator
Efficiency is calculated with:
An efficiently designed system can achieve well over 80% efficiency, resulting in considerable savings of operating costs.
Improving Evaporator Efficiency
To improve MEE efficiency:
- Feed Temperature Optimization: Preheat the feed to minimize steam consumption.
- High-Performance Heat Exchangers: Enhances heat transfer efficiency.
- The Appropriate Vacuum Level: Boosts evaporation rates.
- Reduce Scaling and Fouling: Ensures consistent performance.
Multiple-Effect Evaporators in India
The country has adopted very fast multiple-effect evaporator systems, especially in ZLD systems and wastewater treatment. Manufacturers are coming up with solutions to make very competitive and efficient MEE solutions as per the industrial need.
Multiple-Effect Evaporator Manufacturing
The primary focus of leading manufacturers is on:
- Selection of advanced materials: alloys and stainless steel resistant to corrosion.
- Integration of automation: smart sensors and monitoring with IoT.
- Individualization in Design: custom-made for the specific needs of the industry.
Conclusion
Essentially, a multiple-effect evaporator does wonders for industries that are up for efficiency improvements and cost reductions. MEEs provide all the significant extra benefits against the classical evaporators, like latent heat reuse, optimized feed systems, and advanced manufacturing techniques. One has to invest in an MEE system for continuous sustainability and savings, alongside enhancing operational efficiency.
To meet constantly changing requirements in the industry, an MEE is a good investment to maximize efficiency and value.
Maximizing Industrial Efficiency with Multi-Effect Evaporators
Multi-effect evaporators
In today’s fast-paced industrial culture, efficiency, sustainability, and cost-effectiveness are the key factors determining operational success. In many respects, Multi-Effect Evaporators (MEEs) have become game-changers in secondary industries by providing energy-efficient means for water removal and concentration processes. This blog will explain the importance, applications, advantages, and major design considerations connected with MEE systems, which should help industries increase their performance in evaporation processes.
What is a Multi-Effect Evaporator?
Multi-effect Evaporation (MEE) is an advanced technology for extracting water from a liquid feed in multiple evaporators with sequenced outputs. Heat energy from one effect is used to operate the next effect, minimizing energy consumption. This method is preferably used for very large evaporation industries.
Benefits of Multiple Effect Evaporators (MEE)
- Energy Efficient: It recycles heat between various stages resulting in an overall reduction in energy consumption.
- Cost Effective: The operating cost is lowered by reducing fuel consumption.
- Higher Concentration Capability: Increases the efficiency of liquid concentration.
- Eco-Friendly: Less carbon footprint owing to optimized use of heat.
Three-Effect Evaporator Design and Feed Arrangements
Multi-effect evaporators come in different configurations, with feed arrangements playing a critical role in performance. The primary feed arrangements include:
- Forward Feed: The feed moves in the same direction as steam flow, suitable for temperature-sensitive liquids.
- Backward Feed: The feed flows opposite to the steam direction, ideal for high-viscosity liquids.
- Mixed Feed: A combination of both forward and backward feed mechanisms
Comparison Table: Forward Feed vs. Backward Feed Arrangement
Parameter | Forward Feed | Backward Feed |
Energy Efficiency | Moderate | High |
Suitable for | Low-viscosity liquids | High-viscosity liquids |
Operating Cost | Lower | Slightly Higher |
Heat Utilization | Gradual | More efficient |
Applications of Multi-Effect Evaporators (MEE)
MEE systems are widely used across various industries, including:
- Dairy Industry: Concentration of milk and whey.
- Chemical Processing: Evaporation of solvents and chemical solutions.
- Wastewater Treatment: Effective water removal for industrial effluent management.
- Pharmaceutical: Central concentrated medicated aggregates.
- Food Processing: Dehydrating fruit juices and syrups.
Choosing the Right Multi-Effect Evaporator for Your Application
Choosing the best MEE system depends on several factors:
- Volumetric capacity: Determine liquid volume expected to be processed.
- Energy consumption: When addressing heat efficiency, other factors should include working expenses.
- Material Compatibility: Ensure resistance to corrosion and chemical interactions.
- Space Constraints: Opt for a design that fits the available installation area.
- Automation Level: Choose between manual, semi-automated, or fully automated systems.
Why Multi-Effect Evaporator for Industrial Efficacy
Advanced evaporation techniques are required for industries to achieve efficiency and cost-effectiveness. MEE systems properly utilize thermal energy, making them crucial in industries where massive-scale liquid concentration and water removal are key. Their advantages of the highest efficiency at a reduced environmental impact make them a significant investment for industries.
Multi-Effect Evaporators: How They Work and Importance
The MEE process involves:
- Heating the initial liquid feed using steam.
- Transferring residual heat to subsequent effects for continued evaporation.
- Collecting the concentrated product while recycling vapor.
- Reusing condensate for further industrial applications.
Advantages Of Incorporating MEE Evaporators In Your Industries
- Energy Saving: Reduced consumption of fuel and electricity
- Productivity Improvement: Faster and more controlled evaporation.
- Cost Reduction: Lower maintenance and operational costs.
- Sustainable Processing: Minimal environmental impact with optimized heat recovery.
Key Differences Between Single and Multi-Effect Evaporators
Feature | Single Effect Evaporator | Multi-Effect Evaporator |
Energy Consumption | High | Lower |
Efficiency | Moderate | High |
Initial Cost | Lower | Higher |
Operational Cost | Higher | Lower |
Considerations for Optimal Multiple Effect Evaporation Equipment Design
- Thermal Efficiency: Inclusion of Heat Exchanges in the Working Object for Enhanced Efficiency.
- Material Selection: To last long, corrosion-resistant metals should be used.
- Automation Features: Integration with control systems for better monitoring.
- Scalability: Modular designs for future expansion.
Why Goldfinch Evaporators Are the Best for Multi-Effect Evaporation Solution:
Goldfinch Evaporators is a the-trustworthy name in the MEE solutions-of-its-in-change world high-quality for its platforms in different industrial applications designs, and commissions-the purpose is to provide custom-made, energy-efficient, and sustainable solutions according to the requirements of your business.
Conclusion:
A step into the future: Industrial Efficiency Called Multi-Effect Evaporator. Multi-effect evaporators are an essential technology in the industrial sector dedicated to improving their efficiency, lowering costs, and reducing pollution. MEE systems are optimal solutions that allow enterprises to transform manufacturing and, at the same time, achieve future sustainability. Goldfinch Evaporators has specific, advanced solutions for industrial requirements if your hunt is for a good MEE evaporator supplier.
Looking for a high-performance MEE system? Contact Goldfinch Evaporators today!
MEE Evaporator Perspective: A Sustainable Method for Treating Industrial Wastewater.
The MEE Evaporator works on the basic principle of evaporation, which separates water from contaminants in industrial wastewater.
Unveiling the Efficiency of Multiple Effect Evaporators
Multi-Effect Evaporators MEE
Multi-effect evaporators are integrated systems employed for the effective evaporation of water or solvent from a feed. In these systems, multiple evaporators are incorporated to achieve better energy efficiency to the level that the vapor produced in the first stage is used to heat the subsequent stage. MEEs are widely recognized for their ability to minimize operational costs and optimize energy usage.
What is a Multiple Effect Evaporator?
A Multiple Effect Evaporator involves the structured sequencing of evaporators to remove water from a liquid feed through evaporation. The system leverages the principle of reusing vapor energy from one stage to the next, significantly reducing the need for external energy sources.
Three-Effect Evaporator Design Feed Arrangement
Three-effect evaporators are configured to maximize energy efficiency and accommodate varying feed requirements. The primary feed arrangements include:
- Forward Feed: The liquid flows in the same direction as the vapor, ensuring energy efficiency for feeds that are heat-sensitive.
- Backward Feed: The liquid moves opposite to the vapor flow, which is ideal for concentrated feeds.
- Mixed Feed: A combination of forward and backward feeds for tailored applications.
Applications for Multiple Effect Evaporators
MEEs are employed across various industries for:
Dairy and food processing involves the concentration of milk, juices, and other fluids.
Pharmaceuticals are used for extracting the active ingredients and concentrating solutions.
Chemical processing involves solvent recovery and separation of chemicals.
End treatment of industrial waste becomes volume reduction and recovery of useful materials.
Multiple Effect Evaporators (MEE) for Industrial Wastewater
Industrial wastewater treatment is one of the most critical applications of MEEs. These systems effectively reduce the volume of waste by separating water and contaminants, enabling industries to meet stringent environmental regulations and reduce disposal costs.
Forward Feed Multiple Effect Evaporator
Forward feed systems are ideal for liquids with low boiling points and heat-sensitive properties. The liquid feed enters the first evaporator and flows in the direction of the vapor, ensuring consistent heat transfer and reduced thermal degradation.
Backward Feed Multiple Effect Evaporator
Backward feed systems are designed for highly concentrated or viscous feeds. The liquid moves opposite to the vapor flow, ensuring effective heat transfer and optimal concentration levels.
Forward Feed vs. Backward Feed Arrangement Design
Feature | Forward Feed | Backward Feed |
Direction of Flow | Liquid and vapor flow in the same direction. | Liquid and vapor flow in opposite directions. |
Energy Efficiency | Suitable for heat-sensitive feeds | Ideal for concentrated or viscous feeds. |
Thermal Efficiency | High | Moderate to high depending on application. |
MEE Evaporator Principle
The principle behind MEE systems is the sequential reuse of vapor energy. By utilizing the vapor from one evaporator to heat the next, MEEs achieve substantial energy savings and operational efficiency.
Considerations for an Optimal Multiple Effect Evaporation Equipment Design
Efficient MEEs are designed with the following considerations:
- Heat Transfer Efficiency: Enhanced by selecting materials with high thermal conductivity.
- Liquid-Vapor Separation: Ensures effective separation to improve product quality.
- Energy Efficiency: Incorporates vapor recompression and advanced control systems.
What is the best multiple-effect evaporator for wastewater treatment?
The best MEE for wastewater treatment depends on factors such as feed composition, required concentration, and energy efficiency needs. Goldfinch’s range of MEEs offers tailored solutions to meet industrial requirements.
Why Use Multiple Effect Evaporators?
MEEs are indispensable for industries aiming to:
- Achieve energy efficiency.
- Reduce waste volume.
- Recover valuable by-products.
- Meet environmental regulations
Energy Savings Using MEE Evaporation System
MEE systems significantly reduce energy consumption by reusing vapor energy across multiple stages. This reduces operational costs and carbon footprints, making them a sustainable choice.
Advantages of Forced Circulation MEE Evaporators
Forced circulation MEEs enhance performance through:
- Improved Heat Transfer: Facilitates the handling of viscous liquids.
- Reduced Fouling: Minimizes scaling and ensures consistent operation.
- High Efficiency: Ideal for feeds with high solid content.
Conclusion: The Future of Evaporation Technology
Goldfinch Evaporators have been at the forefront of MEE technology in India for over four decades. Specializing in innovative vapor recompression solutions, Goldfinch’s MEEs deliver unparalleled efficiency and performance across industries. Explore our compact range of MEEs designed to revolutionize wastewater treatment and industrial processes.
To know More Visit This Link –
Explore Multiple Effect Evaporators: Benefits & Applications
Goldfinch Evaporators is an innovator in offering ingenious designs of MEE systems that promise the best to its clients as far as the performance of MEE systems in different industrial applications is concerned. Goldfinch Evaporators has been at the forefront for over forty years in the field of MEE technology.
A Complete Analysis of the Multiple Effect Evaporator Operating Principle (MEE)
Multiple Effect Evaporators (MEE) – Overview
Multiple-effect evaporators (MEE) are extremely useful in industries that require systems for effective evaporation, such as effluent treatment, food processing, and chemical manufacturing. Goldfinch Evaporators is one of the renowned and advanced manufacturers and suppliers of evaporators and related products that work optimally with minimum energy consumption.
What Is a Multiple Effect Evaporator?
A multiple-effect evaporator is a system dedicated to the evaporation of water or any aqueous solution, employing steam as a driving energy source. The system contains several stages, or effects in which each effect is operated at a lower pressure and temperature than the previous one. Such a design helps to save a lot of energy, which is why it is well suited to industries that require evaporation processes that are economical in energy costs.
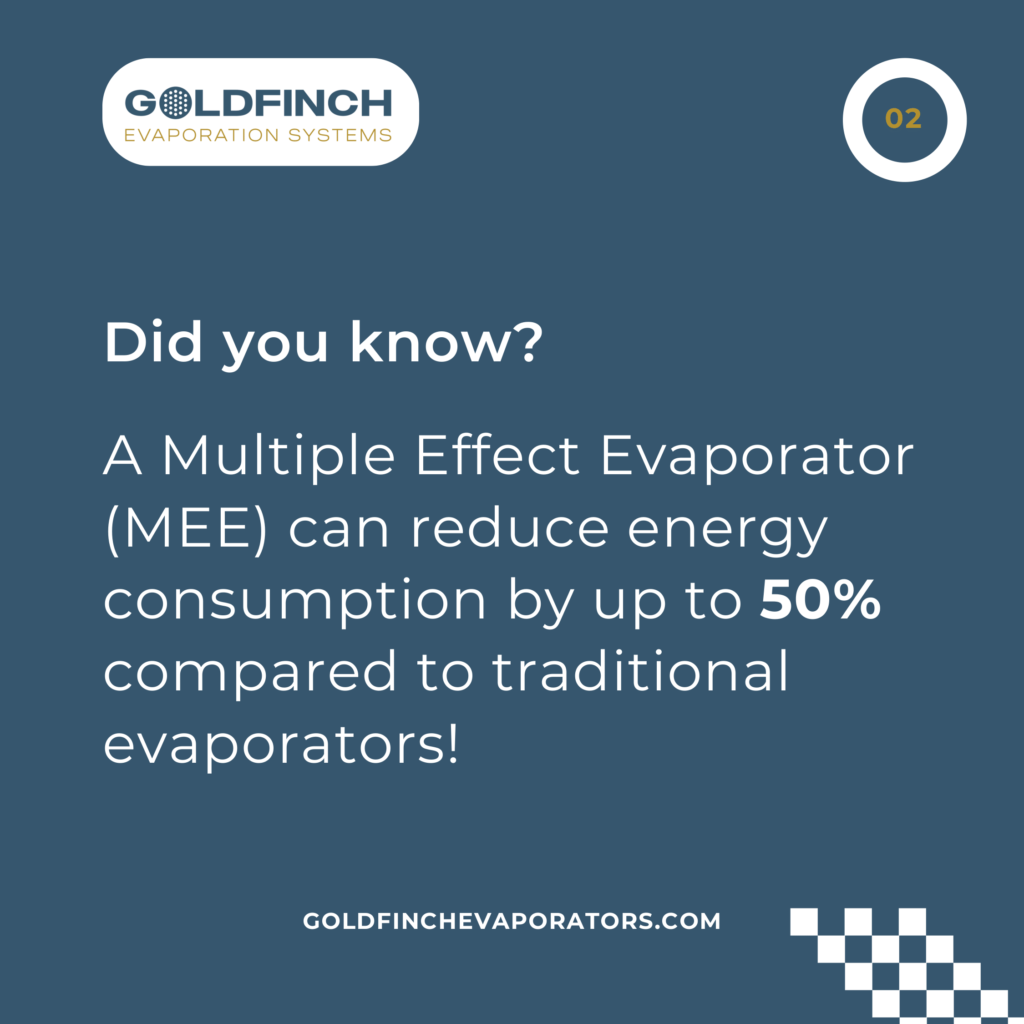
Functioning Principle of Multiple Effect Evaporators
The core concept is primarily based on the recovery of thermal energy and its efficient usage. Water vaporization occurs when steam supplied to the first effect preheats the feed solution. The resulting vapor is subsequently used as a heating medium for the next effect, and this goes on for several stages.
Key Components:
Feed Tank: Stores the solution to be evaporated.
Feed Pump: Ensures a consistent flow of the solution into the system.
First Effect Vapor Separator: Separates the vapor from the concentrated liquid.
Condensers: Condense the vapor into liquid form for reuse or disposal.
Classes of Feed Arrangements in MEE
Forward Feed: In this system, the feed enters in the same direction as the vapor. This is appropriate when dealing with hot solutions as it saves energy.
Backward Feed: In this case, the feed enters in the opposite direction to the vapor flow; this is appropriate for cold solutions.
Parallel Feed: When all effects are in operation, the feed is fed in all at once; this is suitable for processes requiring constant concentration throughout.
Benefits of Using Multiple Effect Evaporators
Energy Efficient: Utilizes heat energy through various stages resulting in lowered steam.
Economical: Reduces the cost of energy and market operations.
Scalability: Accommodates to various industrial scales.
Environmental Considerations: Reduces waste and enhances green production practices.
Design Considerations for MEE
Designing an MEE system requires careful attention to several factors:
Heat Transfer Efficiency: Maximizing heat exchange between steam and the solution.
Material Selection: Ensuring corrosion resistance and durability.
Operational Parameters: Tailoring temperature and pressure conditions to specific requirements.
Utilization of Multiple Effect Evaporators
Treatment of Industrial Effluents: Helps in effectively minimizing the quantitative amount of wastewater.
Production of Food: Removes moisture content from liquid food products such as milk and baby foods.
Pharmaceutical Industry: Helps in the clarification of chemical solutions.
Goldfinch: The Qualitative Go-To Company for Your Multiple Effect Evaporators
Goldfinch Evaporators offers an extensive variety of evaporator products and services to suit different industries. Our experience includes the designing, erection, and servicing of evaporators to guarantee the smooth operation of our clients.
Features of Goldfinch Evaporators
Advanced Vapor Separation: Ensures optimal separation of vapor and liquid.
Customizable Feed Arrangements: Supports forward, backward, and parallel feed configurations.
Eco-Friendly Designs: Compliant with environmental regulations.
Robust Construction: Engineered for durability and efficiency.
Conclusions
MEE units have proven their worth in industries where evaporation is carried out optimally at the lowest possible cost and over a minimal environmental footprint. Goldfinch Evaporators is an innovative and sustainable provider with various industrial applications. Businesses must comprehend the working principle, merits, and uses of MEE to better assess and aid their processes.
If you wish to know more about Goldfinch’s solutions, do not hesitate to reach out to us and find out how our offerings would improve your business.
Top Suppliers of Multiple Effect Evaporators in India: Goldfinch Evaporators
Multiple Effect Evaporators in India
Goldfinch Evaporators, a prominent name among Multiple Effect Evaporators in India, is committed to delivering technologically advanced systems for various industrial evaporation processes. Their skills are not limited to MEEs but also include Mechanical Vapour Compression Evaporators (MVRE) and Zero Liquid Discharge (ZLD) systems, among other evaporator technologies. In this blog, with multiple-effect evaporator (MEE) suppliers in India, we will focus on multiple-effect evaporators, looking at their design structure, advantages, and uses, as well as the amazing services provided by Goldfinch Evaporators.
Defining Multiple Effect Evaporator (MEE) What is a Multiple Effect Evaporator (MEE)? MEE systems are advanced evaporation systems that employ several stages or ‘effects’ of evaporation to concentrate solutions in a particular industry. The basic MEE design principle is to return the vapor produced in one effect and use it to heat the next effect, increasing energy usage efficiency. Such a system benefits industries by enabling them to recover and utilize lost resources, reducing energy costs, and protecting the environment.
Goldfinch Evaporators provides several types of MEE systems that meet the needs of different industries and provide high-efficiency performance energy-saving systems.
Benefits of Multiple Effect Evaporators
Benefits of Using Multiple Effect Evaporators Here are some benefits of Multiple Effect Evaporators compared to the normal evaporation systems:
Energy efficiency: The use of vapor from an already used effect to heat the following one in a MEE system lowers the energy utilized for evaporation.
Economically viable: This is because they do not use fuel in excess, and thus, industries spend less on operating costs and still meet maximum concentration targets.
Less Emission: For every other piece of equipment that uses energy, there is always a tendency for emissions will be incurred and thus MEE systems become less emission-intensive.
Less Emission: For every other piece of equipment that uses energy, there is always a tendency for emissions will be incurred and thus MEE systems become less emission-intensive.
Versatility: MEE systems can be increased in size to cater to different industrial applications; starting from the small scale to the large industrial plants.
Goldfinch Evaporators provides custom-designed MEE systems to fulfill specific operational needs to guarantee maximum efficiency and effectiveness of the system.
Types of Multiple Effect Evaporators
Designs for Multiple Effect Evaporators (MEE) – many types of Multiple Effect Evaporators are designed and manufactured to suit the different requirements of different industrial sectors. The following are the popular designs used:
Forward Feed MEE Design: Here, the feed solution enters the first effect, and the vapor of the next effect is then used to heat the first effect, and so on. This arrangement is used od high-boiling solutions. This design is most commonly used in chemical, pharma, and food processing tubes.
Backward Feed MEE Design: In this design, the feed solution is fed into the last effect, and the vapor flows in a reversed way to warm the solution. This design is useful in processes that produce solutions that are easy to scale, and thus, require a little bit more precautions in the supply of heat. Its common uses include the dairy, sugar, and waste management aspects.
Forward Feed vs. Backward Feed Design: Each design has its pros and cons regarding what solution is being processed. The forward feed feeding system is more energy efficient whereas the backward feed system is better in terms of controlling the fouling amenable materials and also thermal sensitivity materials.
Goldfinch Evaporators produces the two systems for different sectors to be able to choose the best system suitable for their needs.
Multiple Effect Evaporators (MEE) Applications
Multiple Effect Evaporators (MEE) Applications: MEE has several applications in many sectors, including:
Chemical processing: MEE systems are designed and applied in the chemical industry to thicken solutions, extract expensive solvents, and mitigate effluent.
Food and Beverages: MEEs are also utilized in concentrating juice, milk, and other liquid products for longer shelf lives and better quality.
Pharmaceuticals: This applies to Thrombin and other medicines which are ultimately manufactured using lattices. MEEs are employed when hygroscopic and thermostable active ingredients have to be concentrated to the required level of the finished medicine.
Effluent Treatment: Sewage treatment plants also make use of MEE systems to perform desalination and also turn to MEE systems where it is required to conform to ZLD policies.
Dairy and Sugar Industries: These industries utilize MEEs to effectively process concentrates and raw liquids such as milk, sugar solutions, and other viscous effluents.
Goldfinch Evaporators provides the design and manufacture of MEEs for these and other industries for maximum efficiency and adherence to industry requirements.
Mechanical Vapour Recompression Based Evaporators (MVRE)
Evaporators based on Mechanical Vapour Recompression (MVRE) Goldfinch Evaporators brings yet another cutting-edge technology Known as Mechanical Vapour Recompression (MVRE). The use of MVRE is to improve energy efficiency by using mechanical compression to reuse vapor to heat the incoming feed solution. This technology is most beneficial in situations, which call for a great deal of energy savings.
Wastewater treatment strategies
Zero Liquid Discharge Systems Wastewater treatment strategies such as Zero liquid discharge (ZLD) are centered on the policy goal of preserving water resources, to the extent that no liquid discharge is possible. However, ZLD systems are very useful for sectors such as textiles, chemicals, food, etc where waste disposal is a must. Advanced Zero Liquid Discharge systems are provided by Goldfinch Evaporators where industries can adhere to the environmental requisites without compromising on the reclamation of important resources from process wastewater.
Considerations for Optimal Multiple Effect Evaporator Design
Considerations for Optimal Multiple Effect Evaporator Design When selecting the best Multiple Effect Evaporator, it is important to take note of the following aspects:
Feed Characteristics: The characteristics of the condensed medium being processed (viscosity, boiling point, potential for scaling) influence beaucoup the MEE design.
Energy Efficiency: Project the energy requirements and energy savings potential of the system to ensure that the system is economically viable in the long run.
Scale of Operation: The design of MEE should be such that it can be easily decommissioned for a larger or smaller scale of operation.
Fouling Control: In light of the feed solution, which is more likely to be fouling: forward feed or backward feed? Justify your answer.
Automation and Monitoring: Advanced MEEs should incorporate the installation of automatic monitoring and control systems based on performance.
Goldfinch Evaporators ensures that all these aspects area wise considered in the design and manufacturing process to provide the best MEE solutions for the customers.
Which Multiple Effect Evaporator is most advantageous in the treatment of Wastewater?
Which Multiple Effect Evaporator is most advantageous in the treatment of Wastewater? In the case of wastewater treatment applications, the optimum MEE system varies with the physical and chemical properties of the wastewater. For example, Solar Evaporators’ latest ZLD system integrated with a specific design of MEE is one of the best approaches to treat and reclaim water with minimal effects on the environment. Goldfinch Evaporators also offers customized solutions in MEE and ZLD systems which are very efficient and eco-friendly.
To conclude,
Goldfinch Evaporators is a recognized provider of Multiple Effect Evaporators in India specializing in creative solutions for various industries. Goldfinch focuses on MEE, MVRE, and ZLD technologies so that companies can implement energy-saving, environmentally friendly, and cost-effective solutions for their evaporation problems. Be it a Forward Feed MEE system a Backward Feed MEE system or a ZLD system for wastewater treatment, Goldfinch Evaporators has the skills and technology to accomplish any task.
For all your multiple-effect evaporator systems and any other service that relates to them, Goldfinch Evaporators is undoubtedly the best partner to work with.
To Know More Visit This Blog – https://goldfinchevaporators.com/case-study-multiple-effect-evaporator-for-specialty-chemicals-company-in-jhagadia-gujarat/
Case Study : Multiple Effect Evaporator for Specialty Chemicals Company in Jhagadia, Gujarat
Advanced technologies are applied toward the management of wastewater, to meet the stringent environmental norms and sustainable practices. One such technology powerhouse utilized for the efficient treatment of industrial effluent is the Multiple Effect Evaporator (MEE). In the below case study, we discuss the installation and benefits derived from a 150 KLD Four Effect Evaporator installed for one of the reputed specialty chemicals companies based in Taloja.
What is Multiple Effect Evaporator (MEE)?
A multiple-effect evaporator is a sophisticated system designed to concentrate solutions, especially in industries where the question of wastewater treatment is of essence. Basically, MEE works in such a way that steam produced in one evaporator is used to heat up the next, thus saving energy while improving efficiency. This successive evaporation hence reduces the total energy consumption of the process compared with single-stage evaporators.
Overview of the Project
Client and Location
Our customer is a specialty chemicals manufacturer based at Jhagadia, Gujarat. Specialty chemicals of this company are manufactured through a process that involves large amounts of process effluent which needs effective treatment.
Challenges Faced
Several problems related to wastewater management from the client’s manufacturing processes had to be overcome. The effluent production volume was huge, with high levels of TDS, for which an effective and sustainable treatment solution was required. The traditional techniques are not able to manage such a complex composition of effluents, hence compelling the need for an advanced evaporation system.
Solution: Four Effect 150 KLD Multiple Effect Evaporator
Goldfinch Evaporation Systems suggested and installed a Four Effect 150 KLD Multiple Effect Evaporator designed to specifically undertake the complex wastewater stream from the client’s manufacturing processes. This system is engineered for treating a mixture of manufacturing effluent and Reverse Osmosis (RO) reject to offer full treatment and resource recovery in an efficient manner.
System Design and Operation
The Four Effect 150 KLD Multiple Effect Evaporator consists of four effects of evaporation. The steam generated in every effect is re-used in succeeding effects, thereby providing better energy efficiency of the system. This makes sure that there is an effective concentration of the effluent, reducing the volume of the same substantially, along with recovering byproducts of value from it.
Effluent Treatment Optimisation
Evaporator ingeniously designed to process a feed TDS level of about 70,000 ppm. This shall permit the system to address high-salinity wastewater and thus address one of the main concerns of the client.
Salt Recovery Process
The concentrated effluent is further settled in a salt settler and centrifuged to reclaim Sodium Sulphate and organic salts. This step helps not only towards increasing sustainability by decreasing one amount of waste but also provides cost efficiency by recovering and re-using some valuable by-products.
Key Advantages of Multiple Effect Evaporator
Energy Efficiency
One of the major advantages of the multiple-effect evaporator system is its energy efficiency. By reusing the steam in subsequent series, the MEE significantly reduces the energy consumed, thus being cost-effective for industries handling a large volume of wastewater. This feature of saving energy is especially useful in the specialty chemicals industry, where the costs of energy are very high.
Environmental Impact
The Multiple Effect Evaporator system forms an important contribution towards the environment by lessening the impact from industrial operations. By concentrating the wastewater, the volume of effluent that needs to be disposed reduces drastically in volume. This minimization will help in protecting the local water bodies and ecosystems from potential contamination. Further, the recovery and condensate reuse enhance the sustainability quotient of the operation.
Saves Operational Cost
Directly, the reduced energy consumption leads to lower operation costs. This will help industries save a good amount of money on utility bills and provide a multiple-effect evaporator system as economically viable for the long run. Moreover, the re-use of the condensate in the manufacturing process reduces the demand for freshwater, which again adds up to the cost efficiency.
Sustainability and Compliance.
The choice of a multiple-effect evaporator for the specialty chemicals company in Jhagadia was driven by the requirement for a robust and efficient solution to deal with high TDS effluent. It was important for compliance with stringent environmental regulations that the system delivered very good performance for the reduction of wastewater volume and the reusability of treated water.
Why Goldfinch Evaporation Systems?
Goldfinch Evaporation Systems leads in design and implementation of advanced evaporation technologies. Our commitment to innovation, quality, and sustainability has made us a valued partner for industries in need of reliable and proven solutions for the treatment of wastewater.
Experience and Expertise
Our team has gathered the necessary technical potential during years of working with such projects to manage challenging wastewater treatment projects. This large amount of gained experience ensures that we will come up with solutions tailor-made to suit clients’ unique needs.
Tailor-Made Solutions
As we know, all our clients are special and so are their needs. Hence these solutions are valued as specified needs. To optimally and effectively perform, the 150 KLD Four Effect Multiple Effect Evaporator that we worked on for our client from Jhagadia stands as a testimony of our capability to deliver customized and effective wastewater treatment solutions.
High-end Technology
Goldfinch employs the advanced possibilities of evaporation technology to ensure systems that are high in efficiency and friendly to the environment. Our multiple-effect evaporators with up to four effects guarantee the highest possible water recovery and energy efficiency, thus making them ideal for those industries with large volumes of wastewater.
Comprehensive Aftermarket Support
No matter the project, we have you covered from initial consultation to post-installation support. We have a team of experts to support all our clients, starting with system design to implementation and further maintenance.
Conclusion
The installation of the Four Effect 150 KLD Multiple Effect Evaporator at a specialty chemicals company in Jhagadia, Gujarat, points out clearly how the next generation of wastewater treatment technologies can bring a paradigm shift. Adoption of the Multiple Effect Evaporator at the client’s end brought forward good operational efficiencies, a reduction in adverse environmental impacts, and compliance with stringent regulations.
At Goldfinch Evaporation Systems, we are proud to be a part of this successful venture with the client. Our commitment to the provision of state-of-the-art solutions across various industries, tailor-made to each one’s needs, has not wavered in any way.
Follow Goldfinch Evolution Systems on LinkedIn to hear more about our innovation in wastewater treatment solutions and stay up-to-date on our most recent projects underway. Reach out and contact us today to find out how we can support you in managing your waste treatment processes to achieve your SDGs. Together, we create a cleaner, more sustainable world.
Follow us on LinkedIn and contact us for all your wastewater treatment needs.
https://www.linkedin.com/company/goldfinch-evaporation-systems-private-limited/
To Know More Visit This Link – https://goldfinchevaporators.com/a-simplified-comparison-mee-vs-mvre/
A Quick Guide: Evaporators in Wastewater Treatment
Wastewater treatment is a critical process for industries worldwide, and evaporators play a pivotal role in managing liquid waste effectively. At Goldfinch Evaporation Systems, we specialize in providing advanced evaporator solutions tailored for wastewater treatment applications. In this guide, we’ll explore the various types of evaporators and their crucial role in wastewater treatment processes.
At Goldfinch Evaporation Systems, we specialize in advanced evaporator solutions for wastewater treatment. Evaporators are essential for reducing the volume of wastewater by turning liquid into vapor, making waste easier to manage and dispose of. Here, we’ll explain the different types of evaporators and their applications in various industries.
Types of Evaporators
Natural Circulation Evaporators
Natural circulation evaporators rely on the natural movement of liquid caused by density differences. These systems are simple and cost-effective, ideal for small to medium-scale operations with low to moderate solid content.
Forced Circulation Evaporators
Forced circulation evaporators use pumps to circulate the liquid, providing better control over the evaporation process. They are suitable for treating wastewater with high viscosity or high concentrations of suspended solids. These systems ensure uniform heat distribution and reduce fouling, enhancing efficiency and longevity.
Falling Film Evaporators
Falling film evaporators create a thin film of liquid that flows over heated tubes, promoting rapid evaporation. These systems are highly efficient and ideal for heat-sensitive materials, commonly used in food processing, pharmaceuticals, and chemical industries.
Rising Film Evaporators
Rising film evaporators create a film on the inside of vertical tubes, where the liquid rises due to vapor generation at the bottom. This type is effective for low-viscosity liquids and provides high heat transfer efficiency, often used in the dairy and beverage industries.
Multiple Effect Evaporators (MEEs)
Multiple effect evaporators use vapor from one effect to heat the next, significantly improving energy efficiency. This design is ideal for large-scale operations where energy conservation is crucial, such as in desalination, pulp and paper, and chemical manufacturing industries.
Mechanical Vapor Recompression Evaporators (MVRs)
Mechanical vapor recompression evaporators recycle vapor by compressing it to a higher pressure and temperature, using it as a heating medium. This process drastically reduces energy consumption and operational costs. MVR evaporators are suitable for industries with stringent environmental regulations and high wastewater volumes.
Applications in Wastewater Treatment
Evaporators are used in various industries to manage wastewater effectively. Here are some key applications:
Chemical Industry
In the chemical industry, wastewater often contains hazardous substances that need careful handling. Evaporators, especially MEEs and MVRs, concentrate and reduce the volume of these waste streams, making them safer and more economical to dispose of or recycle.
Food and Beverage Industry
The food and beverage industry generates significant volumes of wastewater with high organic content. Falling film and rising film evaporators are particularly effective in this sector due to their efficiency and ability to handle heat-sensitive materials. These systems help reduce waste volume and recover valuable by-products.
Pharmaceutical Industry
Pharmaceutical wastewater contains various organic and inorganic compounds. Evaporators are used to concentrate these waste streams, enabling easier disposal and recovery of solvents. Falling film evaporators are favored due to their gentle handling of temperature-sensitive compounds.
Pulp and Paper Industry
The pulp and paper industry produces large volumes of wastewater with high solid content. Multiple effect evaporators are commonly used to concentrate black liquor, a by-product of the pulping process. This reduces waste volume and recovers valuable chemicals for reuse in the production process.
Mining Industry
Mining operations generate wastewater containing heavy metals and other contaminants. Forced circulation and mechanical vapor recompression evaporators are used to treat these waste streams, reducing their volume and recovering clean water and valuable minerals.
Benefits of Using Evaporators in Wastewater Treatment
Utilizing evaporators in wastewater treatment offers several advantages:
- Volume Reduction: Evaporators significantly reduce the volume of wastewater, making it easier to manage and dispose of.
- Resource Recovery: They enable the recovery of valuable resources from wastewater, such as chemicals and minerals.
- Energy Efficiency: Modern evaporators are designed to be energy-efficient, reducing operational costs.
- Environmental Compliance: Evaporators help industries comply with stringent environmental regulations by reducing the volume and toxicity of wastewater.
- Improved Process Efficiency: By selecting the appropriate type of evaporator, industries can optimize wastewater treatment processes for better performance and reliability.
Choosing the Right Evaporator
Selecting the right evaporator involves considering several factors:
- Type and Characteristics of Wastewater: The composition of the wastewater, including its chemical and physical properties, plays a crucial role in determining the most suitable type of evaporator.
- Capacity and Scale of Operation: The scale of the wastewater treatment operation influences the choice of evaporator. Large-scale operations benefit from the energy efficiency of MEEs and MVRs, while smaller operations may find natural circulation or single-effect evaporators more appropriate.
- Energy Consumption and Efficiency: Energy consumption impacts operational costs. MEEs and MVRs offer superior energy efficiency, making them ideal for industries where energy costs are a significant concern.
- Maintenance and Operational Costs: Different evaporators have varying maintenance requirements and operational costs. Choosing a system with lower maintenance needs can reduce long-term expenses.
- Environmental Impact: The environmental impact of the evaporator system should be considered. Energy-efficient systems not only reduce operational costs but also minimize greenhouse gas emissions.
At Goldfinch Evaporation Systems, we are dedicated to providing cutting-edge evaporator solutions tailored to your specific needs. Our expertise in design, manufacturing, and implementation ensures efficient, reliable, and cost-effective systems.
Customized Solutions
We understand that each wastewater treatment challenge is unique. Our team works closely with clients to develop customized evaporator solutions that meet their specific requirements, ensuring optimal performance and efficiency.
Cutting Edge technology
Goldfinch Evaporation Systems utilizes the latest advancements in evaporator technology. Our systems incorporate innovative features that enhance energy efficiency, reduce maintenance requirements, and improve overall performance.
Sustainability Focus
Sustainability is at the core of our operations. We are committed to developing evaporator systems that not only meet regulatory requirements but also contribute to long-term sustainability by minimizing waste and conserving resources.
Comprehensive Support
Our relationship with clients extends beyond the installation of evaporator systems. We offer comprehensive support services, including regular maintenance, troubleshooting, and optimization, to ensure that our systems continue to operate at peak efficiency.
In house manufacturing unit
Conclusion
Evaporators are vital for effective wastewater treatment, offering numerous benefits such as volume reduction, resource recovery, energy efficiency, and environmental compliance. Goldfinch Evaporation Systems is committed to delivering top-quality evaporator solutions that address the unique challenges of wastewater treatment. With a focus on innovation, customization, and sustainability, we help our clients achieve their environmental and operational goals.