Introduction: The Importance of MEE Evaporators
Industries across India and the world are increasingly focusing on environmental sustainability and energy efficiency. Due to this, advanced technologies like the MEE evaporator have become vital. From wastewater treatment to product concentration, multiple effect evaporation is helping industries cut costs and meet compliance standards without sacrificing performance.
A Multiple Effect Evaporator (MEE) is a thermal separation technology that uses the principle of vapor reuse to concentrate liquids while minimizing steam consumption. Whether you’re in pharmaceuticals, food processing, textiles, or chemicals, adopting a high-quality MEE evaporator system by Goldfinch Evaporators can enhance your operational efficiency significantly.
What is a MEE Evaporator and How Does it Work?
Goldfinch‘s MEE evaporator is designed to use the vapor generated in one stage/ effect to heat the subsequent stage, allowing multiple rounds of evaporation with reduced energy input. This use of vapor drastically reduces the need for fresh steam at each stage, making the process highly efficient compared to single-effect systems.
The typical MEE setup includes a series of vessels, effects, condensers, and heat exchangers that operate under decreasing pressure. As the solution passes through these effects, its water content is reduced, resulting in a concentrated product or reduced effluent volume.
The most remarkable aspect of the multiple effect evaporation process is its ability to extract maximum utility from energy input, making it ideal for industries where energy conservation is critical.
Why Industries Prefer MEE Evaporators
With rising energy costs and tightening environmental norms, industries are increasingly turning to MEE evaporators from Goldfinch for a range of benefits:
1. Energy Efficiency
The reuse of vapor in multiple stages drastically cuts down steam consumption, making the MEE evaporator a standout in energy conservation.
2. Cost-Effectiveness
Lower steam usage and reduced energy bills result in significant operational cost savings over time.
3. Scalability
MEE systems can be customized and scaled to meet the specific requirements of small, medium, or large-scale operations, ensuring long-term flexibility.
4. Regulatory Compliance
Industries dealing with hazardous or large volumes of effluent are increasingly required to comply with zero liquid discharge (ZLD) norms. MEE systems help meet these standards efficiently.
5. Sustainability
By minimizing waste and maximizing resource recovery, MEE evaporators contribute to greener manufacturing practices.
These advantages explain why Goldfinch‘s MEE evaporator is becoming the standard for industries seeking sustainable and cost-effective solutions.
MEE Evaporators in Wastewater Treatment
One of the most crucial applications of the MEE evaporator is in wastewater treatment. Many industries, such as chemicals, textiles, pharmaceuticals, and food processing, generate large volumes of wastewater that cannot be discharged without treatment.
By using multiple effect evaporation by Goldfinch, companies can significantly reduce the volume of effluent by removing water content and isolating valuable or hazardous components. The concentrated residue can be further treated or safely disposed of, while the distilled water can be reused in the process, reducing fresh water dependency.
When integrated into waste water treatment plants, MEE systems offer the following benefits:
- Lower sludge volume
- Improved recovery of reusable water
- Reduction in chemical treatment requirements
- Compliance with ZLD norms
Goldfinch Evaporators designs and manufactures highly efficient MEE systems that are widely used in industrial waste water treatment plants, helping clients meet their environmental and economic goals.
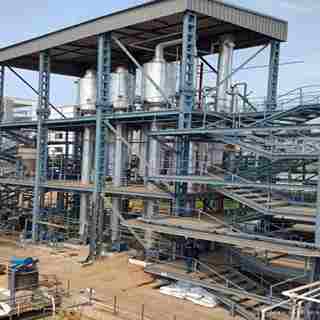
Applications of MEE Evaporators Across Industries
The versatility of MEE evaporators makes them essential across a wide range of industries:
● Pharmaceutical Industry
Used to concentrate active pharmaceutical ingredients (APIs), remove solvents, and ensure drug purity through controlled evaporation.
● Food and Beverage Industry
Ideal for concentrating fruit juices, dairy products, sweeteners, and sauces while preserving flavour and nutritional value.
● Chemical Industry
Helps recover solvents, concentrate solutions, and treat effluents, especially in processes involving corrosive or volatile chemicals.
● Textile and Dyeing Industry
Used to treat dye effluent and recover valuable chemicals, reducing pollution and operational costs.
● Dairy and Sugar Industry
Employed to concentrate milk, sugar solutions, and other viscous liquids for longer shelf life and reduced transportation costs.
These diverse applications make Goldfinch‘s multiple effect evaporators indispensable to modern industry.
Choosing the Right MEE Evaporator Manufacturer
Selecting the right MEE evaporator is just one part of the process. You also need to choose a trusted and experienced manufacturer. You should look for these things:
- Proven Experience
Choose a supplier with a strong track record in designing, manufacturing, and commissioning MEE systems for a variety of industries.
- Customized Design
Every industry has unique processing needs. A reliable manufacturer should offer tailored solutions, whether it’s forward feed, backward feed, or hybrid MEE designs.
- Operational Support
MEE systems are complex to operate. The right partner will offer commissioning assistance, training, and user-friendly automation for smooth operation.
- After-Sales Service
Quick support, spare parts availability, and annual maintenance contracts ensure minimal downtime and long-term reliability.
Goldfinch Evaporators meets all these criteria. With over 50 installations across India, Goldfinch is one of the most advanced evaporator manufacturers in India. Our in-house design team uses advanced thermal design software to deliver optimal capital and operating cost solutions.
Conclusion: Make the Smart Choice with Goldfinch Evaporators
Nowadays, industrial efficiency, cost savings, and sustainability are more important than ever. A MEE evaporator stands out as a reliable and intelligent solution for such scenarios.
Whether you need to treat large volumes of wastewater or concentrate valuable products, investing in a well-designed multiple effect evaporation system by Goldfinch Evaporators can transform your process and reduce your environmental footprint.
Goldfinch Evaporators is one of the leading evaporator manufacturers in India. With cutting-edge technology, customized solutions, and a proven track record, we are the top supplier of industrial evaporation systems in the country.
Check our LinkedIn for more updates.